Linear Motor Driver Control Card COPLEY Brushless Driver For High Response And High Acceleration
Place of Origin | Suzhou china |
---|---|
Brand Name | COPELY |
Certification | ISO9001 |
Model Number | XTL PANEL |
Minimum Order Quantity | ≥1PCS |
Price | $130-$175 |
Packaging Details | carton packaging ect. |
Delivery Time | 1-5 products 5-7 days shipment, samples 3-5 days, bulk to be negotiated |
Payment Terms | T/T |
Supply Ability | Negotiable |
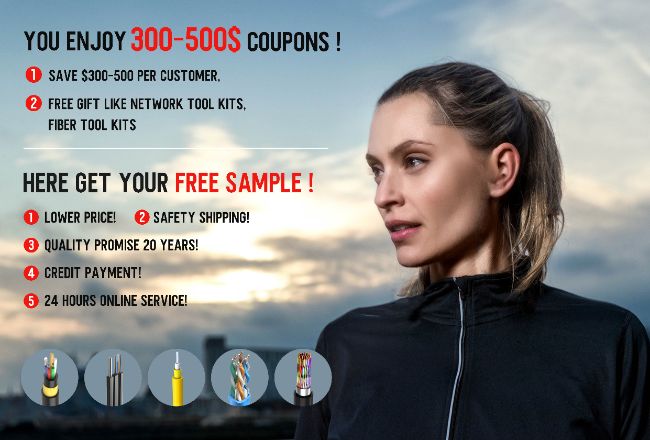
Contact me for free samples and coupons.
Whatsapp:0086 18588475571
Wechat: 0086 18588475571
Skype: sales10@aixton.com
If you have any concern, we provide 24-hour online help.
xSPECIFICATIONS | XTL-230-18 | Weight | 35g |
---|---|---|---|
Overall Dimension | 200*400*602mm | TRAIT | High Acceleration |
Voltage | 220V | Quantity | 9898 |
Power | 36W | ||
Highlight | High Response Servo Motor Controller 36W,Servo Motor Controller COPLEY,Linear Motor Driver Control Card 36W |
Linear Motor Driver Control Card COPLEY Brushless Driver For High Response And High Acceleration
Product Description:
COPLEY brushless driver is a high-performance motor driver designed specifically for industrial automation, robotics, medical equipment, and other precision control applications. The brushless driver adopts advanced brushless motor control technology, which can provide efficient, accurate, and reliable motion control.
COPLEY brushless drivers have multiple superior characteristics. Firstly, they possess high-precision position and speed control capabilities, enabling precise motion control and are suitable for applications that require high precision, such as positioning and assembly on automated production lines. Secondly, brushless drives have efficient energy conversion, reducing energy consumption, and improving system efficiency and sustainability.
In addition, COPLEY brushless drivers have high programmability and flexibility, which can adapt to different application requirements. Users can configure and adjust parameters to achieve different motion modes, acceleration and velocity curves, as well as respond to different external control signals. This flexibility makes it suitable for various application scenarios, from motion control of precision robotic arms to precise positioning of medical imaging equipment.
In addition, the COPLEY brushless driver also has advanced protection and monitoring functions, which can monitor current, temperature, and other key parameters to prevent overload and faults. This helps to extend the lifespan of the equipment and improve the reliability of the system.
In summary, COPLEY brushless driver is an advanced motor control solution with high precision, high efficiency, and flexibility. They play an important role in industries, healthcare, robotics, and other fields, providing stable, accurate, and reliable motion control support for various applications.
COPLEY DRIVE
The drive provides a rich absolute value encoder interface that supports Endat,Biss,SSI and Absolute A Protocols such as. Provide the CMO or CML source code that can be called directly can be developed under Windows and ROST,It can call directly related motion function, that controls the motor according to the specified position speed and time(PNT)curve Perform the motion.
MODEL | AC3-055-09 | ACJ-055-18 | ACJ-090-03 | ACJ-090-09 | AJ-90-12 | ||||
OUTPUT POWER | |||||||||
Peak Current | 9(636) | 18(12.73) | 3(212) | 9(636) | 12(8.5) | Adc(Arms, sinusoidal,±5% | |||
peak time | 1 | 1 | 1 | 1 | 1 | Sec | |||
continuous current | 3(2.12) | 6(4.24) | 1(0.71) | 3(2.12) | 6(4.24) | Adc(Arms,sinuscidal),±5% | |||
Peak Output Power | 490 | 970 | 270 | 800 | 1600 | w | |||
continuous" " | 163 | 323 | 89 | 267 | 533 | w | |||
Output resistance | 0.075 | 0.075 | 0.075 | 0.036 | 0.075 | Rlout(Ω) | |||
Maximum output votage | vout≌HV0.97*Rou*tlout | ||||||||
INPUT POWER | |||||||||
Hv.to Hv. | 20-55 | 20-55 | 20-90 | 20-90 | 20-90 | +vdc,lransfo mer-iolaed | |||
lpeak | 9 | 18 | 3 | 9 | 12 | Adc(1 sec) peak | |||
Icont | 3 | 6 | 1 | 3 | 6 | Adc continuous | |||
Aux HV | 20-HVmax +Vdc @ 500 mAdc maximum | ||||||||
PWM OUTPUTROLS | 3-phase MOSFET inverter ,15 kHz center-weighted PWM, space-vector modulation 3o kHz |
||||||||
Type pwm ripple frequency |
|||||||||
DIGITAL CONTROL | |||||||||
Digital Control Loops |
current,veocity,postion. 100% digital loop control Dual loop position cortrol using secondary encoder input Current loop:15 kHz(66.7 us)Velocity, position loops: 3kHz(333 us) sinusoidal field-oriented control or trapezoidal from Halls for brushliess motors certer-weighted PWH with space-vector modulation current loop:2.5 kHz typical, bandwidth will vary with tuning & load inductance changes in bus voltage do not affect bandwidth 200 uH line-line |
||||||||
samping rate (time) | |||||||||
commutation | |||||||||
Modulation | |||||||||
Bandwidths | |||||||||
HV Compensation | |||||||||
Minimum load inductance | |||||||||
COMMAND INPUTS | |||||||||
CANopen | Profile Position,Interpolated Position, Profile Velocity,Profile Torque,Homing | ||||||||
Digital position | Step/Direction,CW/CCW stepper commands (2 MHz maximum rate) | ||||||||
Quad A/B Encoder | 20 Mcount/sec (after quadrature),5Mline/ sec | ||||||||
Digital torque & velocity | pWM,Polarity | PWM ≌ 0~100%,polarity=1/0 | |||||||
PWM | PWM≌50% ±50%,no polarity signal required | ||||||||
PWM frequency rangr | 1kHz minimum,100kHz maximum | ||||||||
Pw minimum pulse width | 220 ns | ||||||||
Analog torque/velocity/positon | ±10 vdc,5kΩ dirferential input impedance | ||||||||
DIGITAL INPUTS | |||||||||
Number type | 9,non-isolated.[IN1]dedicated to Drive Enable function,[IN2]~[IN9]are programmable 74HC14 Schmitt trigger operating from +5 Vdc with RC filter on input 10 kΩ to +5 Vdc or ground for all except [IN5](see below) Vin-Lo 1.35 Vdc,vin-HI >3.65 vdc All inputs have group selectable connection of input pull-up/ down reslstor to +5 Vdc,or gound 1 Dedicated input with 330 us RC filter for drive enable,0 to +24 Vdc max 3 General Purpose irputs with 330 us RC filter,0 to+24 vdc max 1 Mediun-Speed input for motor temperature switch,33 us RC filtet 4.99 kΩ pullup/pulldown,0 to +24 vdc max 4 High-Speed inputs irputs with 100 ns RC filter,0 to +5 Vdc max |
||||||||
All inputs | |||||||||
Logic levels | |||||||||
Pull-up,pull-down control | |||||||||
Enable[IN1] | |||||||||
GP[IN2,3,4] | |||||||||
MS [IN5] | |||||||||
HS[IN6,7,8,9] | |||||||||
DIGITAL OUTPUTS (NOTE 1) | |||||||||
Numbet type | 4,non-isolated,programmable current-sinking MDSFETwith 1 kΩ pullup to +5 Vdc through diode 300 mAdc max,+30 ve max.Functions programmable External fyback diode requred if driving inductive loads |
||||||||
[OUT1~4] | |||||||||
current rating | |||||||||
current rating |
Why Elmo driver?
Compact and high power density
Multi function and high reliability products
Wide market, wide application
Excellent motion control performance
driver application market
Elmo Motor Introduction
Compact and low cost solutions: torque,speed and position application
Gain type & absolute encoder
Technology:
Elmo's product is a long experience, extensive knowledge and high level
of technology crystallization
Analog power conversion
ASIC based on current loop control
DSP and processor - digital drive
Bus structure - digital drive
Third generation motion control programming language
Advanced installation and debugging technology